The work program is the backbone of any project... but it's also one of the most ignored, outdated, or misused documents in the industry.
And it's not out of bad intention: it's because many times you don't have the right tools or habits to keep him alive.
Here I share you 5 bad practices that we commonly see in the field, and how to avoid them so that your program is a true control tool, not just a requirement.
1. Use Excel as if it were specialized software
Excel is a useful tool, yes... but it was not designed to build industrial buildings or residential buildings.
Using it as the main system for the work program can cause:
- Dependency errors.
- Lack of collaboration.
- Difficulty updating and sharing.
📉 Fact: A Construction Dive study revealed that 70% of projects that are planned only in Excel suffer delays greater than 10% of the estimated time.
How to avoid it?
Use platforms built for work, with dynamic calendars, linked tasks and real-time collaboration.
2. Do not consider unforeseen events or rain.
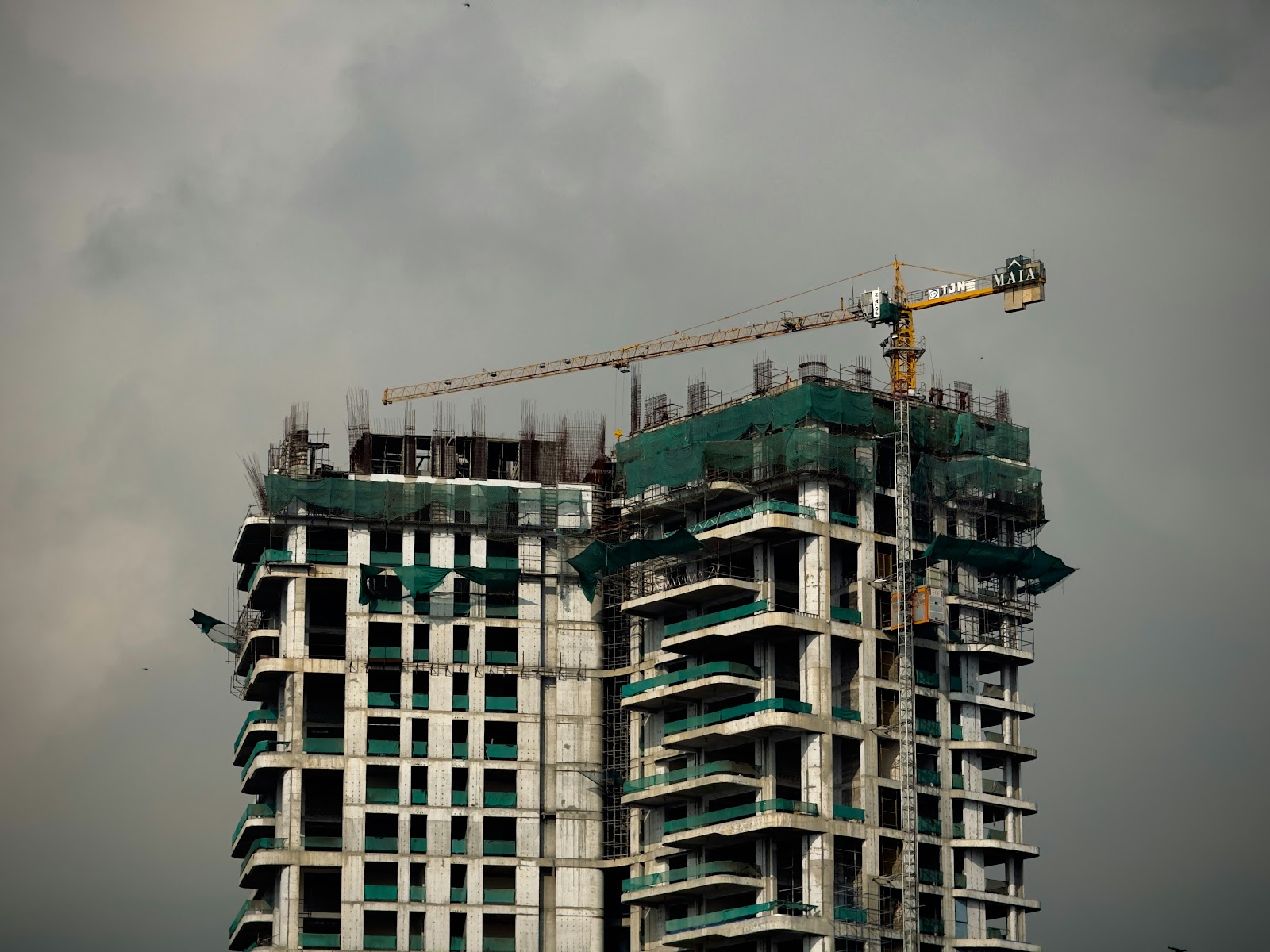
In the rainy season, many programs go down. Literally.
Most programs are built under ideal conditions and do not include:
- Intense rainy days.
- Supply changes.
- Changes by design or customer.
How to avoid it?
Make intelligent buffers. Use historical data. And it updates the program every week, not just when there's a crisis.
3. Update it only once a month
A program that is not constantly updated... it's a mirage.
If you wait until the end of the month to move games, the problems have already caught up with you.
•Contractors are already out of date.
•The customer has already lost trust.
•Your equipment is already putting out fires.
How to avoid it?
Link your program to daily reports, photos, progress and real tasks. The ideal is to have a minimum weekly review.
4. Don't involve contractors in planning
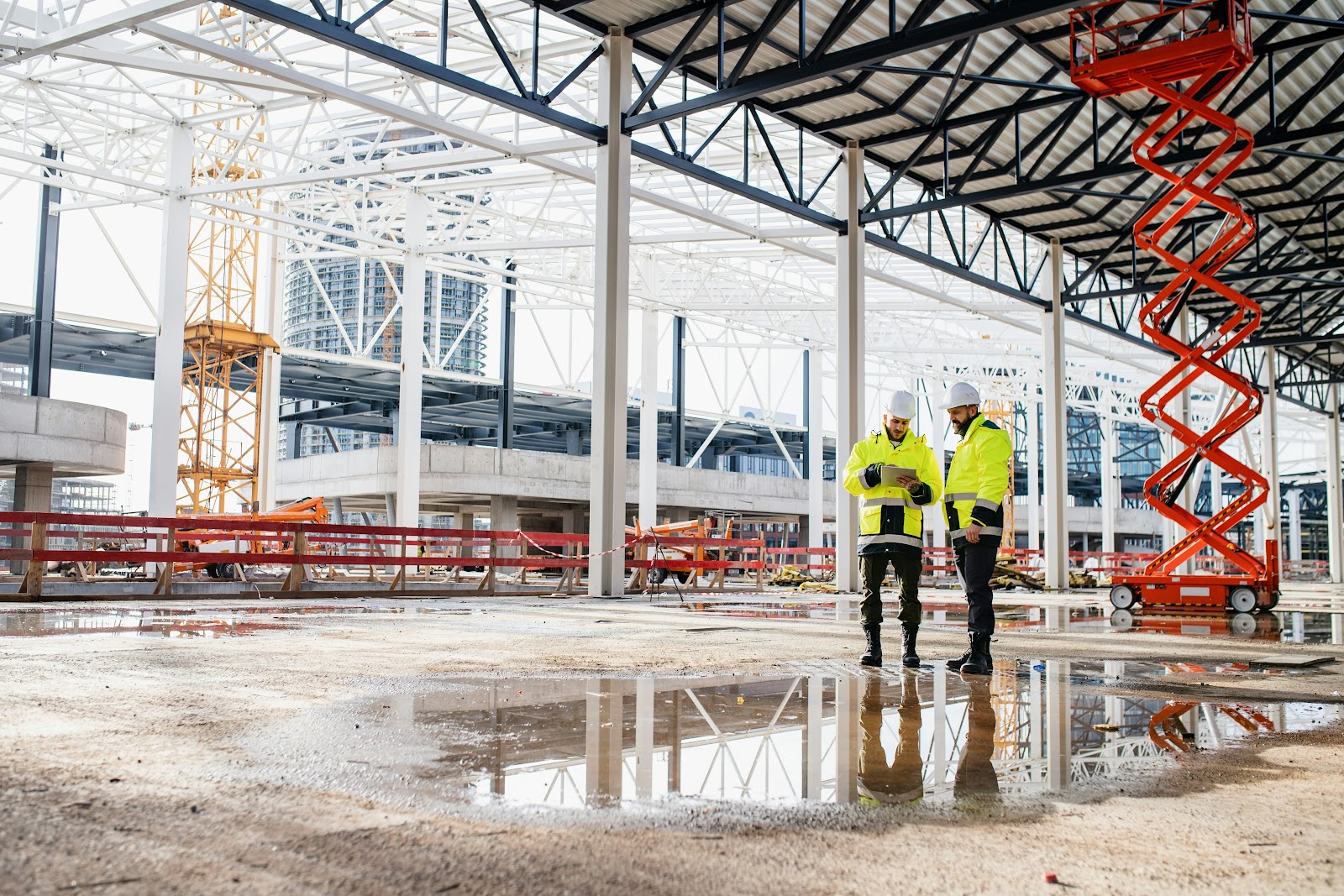
One of the most common mistakes is doing the program between the resident and the PM... without consulting those who are actually going to execute it.
- Unreal times? Probably.
- Poorly thought out sequences? Also.
How to avoid it?
Involve your key contractors from day one. Do collaborative reviews. And let them have their say: they know their performance and their scope for each job.
5. Do not connect the program to the real daily life
A program that lives in a closed file doesn't work.
If you don't connect it to:
- Assigned tasks.
- Physical advances.
- Photos and evidence.
... then it becomes a dead program.
How to avoid it?
Use a platform where what happens on site feeds directly into the program. This way you can compare what was planned vs. what was executed without relying on eternal meetings.
🧠 The solution? A living, collaborative and traceable system
A good work program it's not done just once. It is built every day.
At Buildpeer, we believe that the program should not be an isolated file, but rather a living reflection of the project.
That's why we connect it directly to:
- Daily reports.
- Physical advances with evidence.
- Tasks with managers.
- Supervisory inspections.
- And many more modules...
This not only helps you avoid the 5 bad practices, but also have total control of your time, your contractors and your deliveries.
🎯 Because a good program is not the one that looks the best... but the one that is best fulfilled